SS Checkered Plate Manufacturing Near Peenya
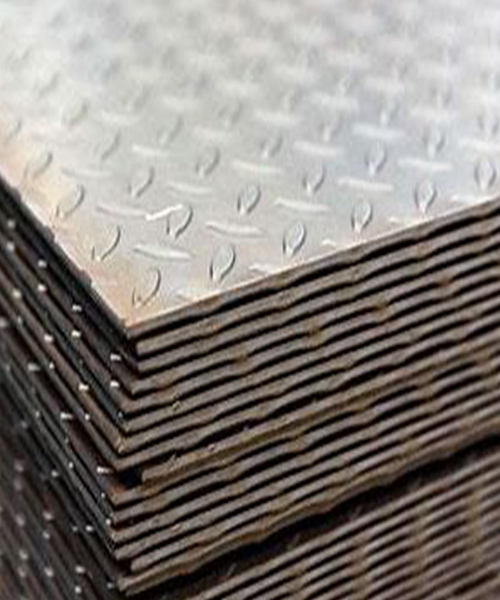
Contact : +919353077501
Stainless Steel (SS) checkered plates are an essential material in various industries due to their durability, corrosion resistance, and non-slip properties. The manufacturing process of SS checkered plates involves several steps, including raw material selection, hot rolling, surface treatment, and quality inspection. These plates are widely used in construction, transportation, and industrial applications, where both strength and safety are paramount.
Raw Material Selection
The manufacturing process begins with the selection of high-quality stainless steel raw materials. Typically, stainless steel grades like 304, 316, and 410 are used for checkered plates due to their excellent corrosion resistance, tensile strength, and workability. These grades are chosen based on the intended application of the checkered plates. For instance, SS 304 is often used for general-purpose applications, while SS 316 is preferred in environments with higher exposure to corrosive elements.
Hot Rolling Process
Once the raw material is selected, it undergoes a hot rolling process. This involves heating the stainless steel to a temperature above its recrystallization point, which is around 1200°C (2192°F) for most stainless steel grades. At this high temperature, the steel becomes malleable, allowing it to be rolled into sheets of the desired thickness. The hot rolling process is crucial because it determines the thickness, strength, and texture of the final product.
Checkered Pattern Formation
The distinctive checkered pattern on the SS plates is formed during the hot rolling process. As the stainless steel sheet passes through the rollers, the pattern is embossed onto the surface of the plate. The pattern, typically in the form of raised diamonds or lines, is what gives the checkered plate its non-slip properties. The depth and spacing of the pattern are controlled to meet specific safety standards, making the plates suitable for use in areas where traction is important, such as stair treads, walkways, and flooring in industrial plants.
Surface Treatment and Finishing
After the checkered pattern is formed, the plates undergo surface treatment to enhance their appearance and corrosion resistance. This typically involves processes like pickling, passivation, and polishing. Pickling removes any oxide scale formed during the hot rolling process, while passivation increases the corrosion resistance by forming a thin oxide layer on the surface. Polishing gives the plates a smooth, reflective finish, which is not only aesthetically pleasing but also easier to clean.
Quality Inspection and Testing
Quality inspection is a critical step in the manufacturing process to ensure that the SS checkered plates meet industry standards. The plates are inspected for thickness, pattern depth, surface finish, and overall dimensions. Non-destructive testing methods, such as ultrasonic testing, are often used to detect any internal defects like cracks or voids. Additionally, the mechanical properties of the plates, such as tensile strength, yield strength, and elongation, are tested to ensure they meet the required specifications.
Applications
Stainless steel checkered plates are used in various applications due to their durability and safety features. In the construction industry, they are used for flooring, stair treads, and wall panels. In transportation, SS checkered plates are commonly used in the manufacturing of bus floors, truck beds, and ramps due to their anti-slip properties. They are also used in industrial environments, particularly in areas where there is a risk of spillage or moisture, as they provide a safe, non-slip surface.
Conclusion
The manufacturing of SS checkered plates involves a combination of precise material selection, advanced rolling techniques, and rigorous quality control measures. The result is a versatile product that offers both functional and aesthetic benefits, making it indispensable in many sectors. With ongoing advancements in stainless steel technology, the production of checkered plates continues to evolve, offering even greater performance and reliability.