SS Fittings Manufacturers Near Peenya
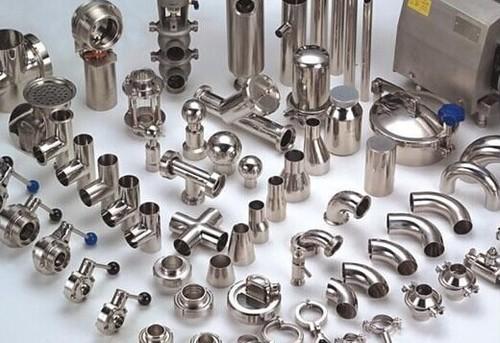
Contact : +919353077501
SS Fittings Manufacturing: An In-Depth Overview
Stainless steel (SS) fittings are critical components in various industries, known for their durability, resistance to corrosion, and aesthetic appeal. The manufacturing process of SS fittings is a complex and meticulous one, involving several stages from material selection to final finishing. This overview will delve into the manufacturing process, key considerations, and the applications of SS fittings.
1. Material Selection
The first step in manufacturing SS fittings is selecting the appropriate grade of stainless steel. Common grades include 304, 316, and 321, each offering different properties suitable for specific applications. For example, SS 304 is widely used due to its excellent corrosion resistance and cost-effectiveness, while SS 316 is preferred in marine and chemical environments for its enhanced resistance to corrosion.
2. Cutting and Shaping
Once the stainless steel grade is chosen, the raw material, typically in the form of bars or sheets, is cut into the required shapes and sizes using various cutting methods. Techniques such as plasma cutting, laser cutting, and shearing are employed depending on the precision required and the thickness of the material.
Plasma Cutting: Plasma cutting involves using a high-velocity jet of ionized gas (plasma) to cut through the stainless steel. It is highly effective for thicker materials and provides a clean cut with minimal finishing required.
Laser Cutting: Laser cutting uses a focused beam of light to cut through the material. It offers high precision and is suitable for intricate shapes and designs, making it a preferred choice for custom SS fittings.
Shearing: Shearing is a mechanical process where a piece of stainless steel is cut by applying a shear force. It is commonly used for cutting straight lines in sheets and is a quick and cost-effective method for producing SS fittings.
3. Forming
After cutting, the next step is forming the stainless steel into the desired shape. This can involve various processes, such as bending, stamping, forging, or extrusion.
Bending: Bending is done using a press brake or a similar tool, where force is applied to bend the stainless steel into the required shape. The bending process is crucial for creating SS fittings such as elbows, tees, and reducers.
Stamping: Stamping involves pressing a sheet of stainless steel into a die to form specific shapes. This process is often used to produce SS flanges, caps, and other fittings that require a high degree of precision.
Forging: Forging is a process where stainless steel is heated and then hammered or pressed into shape. It produces fittings with superior strength and durability, often used in high-pressure applications.
Extrusion: In extrusion, the stainless steel is forced through a die to create long sections of a specific cross-sectional profile. This method is used to produce SS fittings like pipes, tubes, and channels.
4. Heat Treatment
Heat treatment is an essential part of SS fittings manufacturing, as it enhances the mechanical properties of the fittings, such as strength, hardness, and resistance to wear. Common heat treatment processes include annealing, quenching, and tempering.
Annealing: Annealing involves heating the stainless steel to a specific temperature and then slowly cooling it. This process relieves internal stresses, improves ductility, and enhances the material's overall performance.
Quenching: Quenching is the rapid cooling of stainless steel after it has been heated, typically by immersion in water or oil. This process increases the hardness and strength of the SS fittings.
Tempering: Tempering is performed after quenching to reduce brittleness while maintaining the hardness of the stainless steel. The fittings are reheated to a lower temperature and then slowly cooled.
5. Machining
Machining is another critical stage in the manufacturing of SS fittings. This involves various processes such as drilling, milling, and threading to achieve the final dimensions and specifications.
Drilling: Drilling creates holes in the SS fittings for bolts or other connectors. Precision is crucial here to ensure proper fitment in assemblies.
Milling: Milling removes excess material from the fitting to achieve the desired shape and size. It can also create complex geometries that are difficult to achieve through other methods.
Threading: Threading is done to create screw threads on SS fittings, which are essential for assembly in piping systems and other applications. Accurate threading ensures a tight seal and prevents leaks.
6. Surface Finishing
The final step in manufacturing SS fittings is surface finishing. This not only improves the appearance of the fittings but also enhances their resistance to corrosion and wear. Common finishing techniques include polishing, buffing, and passivation.
Polishing and Buffing: Polishing and buffing involve using abrasive materials to smooth the surface of the stainless steel, resulting in a shiny, mirror-like finish. This is particularly important for fittings used in industries where aesthetics are crucial, such as architecture and interior design.
Passivation: Passivation is a chemical treatment that removes free iron from the surface of the stainless steel, enhancing its corrosion resistance. This process is critical for SS fittings used in harsh environments, such as chemical processing or marine applications.
7. Quality Control
Quality control is an integral part of the SS fittings manufacturing process. Each fitting must be inspected for defects such as cracks, deformities, or inconsistencies in material composition. Various non-destructive testing methods, such as ultrasonic testing, X-ray inspection, and dye penetrant testing, are employed to ensure the fittings meet the required standards.
8. Packaging and Distribution
After passing quality control, the SS fittings are cleaned, packaged, and prepared for distribution. Proper packaging is crucial to prevent damage during transit, especially for fittings that have undergone surface finishing.
9. Applications of SS Fittings
SS fittings are used across a wide range of industries due to their versatility and durability. In the oil and gas industry, they are used in pipelines and refinery equipment. In the chemical industry, SS fittings are essential for handling corrosive substances. They are also widely used in the food and beverage industry due to their hygienic properties, as well as in the construction industry for plumbing and architectural purposes.
10. Conclusion
Manufacturing SS fittings is a sophisticated process that requires careful attention to detail at every stage, from material selection to final inspection. The resulting products are vital components in many industries, providing reliable and durable connections that withstand the rigors of demanding environments. As industries continue to evolve, the demand for high-quality SS fittings will only grow, driving innovation and improvements in the manufacturing process.