Stainless Steel Pipes Manufacturers
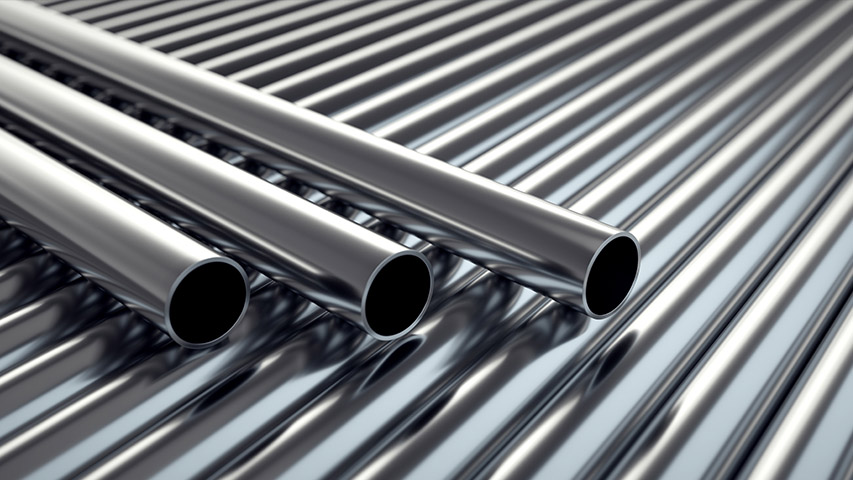
Stainless Steel Pipes Manufacturing: A Comprehensive Overview
Stainless steel pipes are indispensable in numerous industries due to their strength, durability, and resistance to corrosion. The process of manufacturing these pipes involves precise engineering and rigorous quality control to ensure they meet the demands of various applications, including construction, automotive, chemical processing, and more.
Materials Used
The primary material for stainless steel pipes is stainless steel alloy, which consists of iron, chromium, nickel, and other elements like molybdenum or manganese. The high chromium content (usually 10.5% or more) is what gives stainless steel its corrosion-resistant properties. Depending on the intended use, manufacturers may choose specific grades of stainless steel, such as 304, 316, or 430, each tailored for specific applications.
Manufacturing Process
-
Melting and Casting:
- The process begins with melting raw materials in an electric arc furnace. The molten metal is then cast into rectangular shapes called billets or round shapes called blooms.
-
Hot Rolling:
- These billets or blooms are heated and passed through rollers to form a rough cylindrical shape. For seamless pipes, the billet is pierced to create a hollow tube. For welded pipes, flat sheets of stainless steel are rolled and welded together.
-
Cold Rolling and Drawing:
- The hot-rolled pipe undergoes cold rolling or drawing to achieve precise dimensions, smooth surfaces, and improved mechanical properties. This step is crucial for producing high-quality pipes.
-
Welding (For Welded Pipes):
- Stainless steel sheets are formed into cylindrical shapes and welded along the seam using methods such as tungsten inert gas (TIG) or laser welding. Advanced techniques ensure the weld is as strong and corrosion-resistant as the base material.
-
Heat Treatment:
- To enhance strength and corrosion resistance, the pipes undergo annealing—a process of heating and cooling under controlled conditions. This step also eliminates internal stresses caused by welding or rolling.
-
Surface Finishing:
- Pipes are polished or treated to achieve the desired surface finish, such as matte, brushed, or mirror. Surface treatments may also include pickling, which removes any oxide scale or contaminants.
-
Quality Testing:
- Rigorous testing is conducted to ensure the pipes meet industry standards. Tests include:
- Non-destructive Testing (NDT): Ultrasonic or X-ray methods to detect internal flaws.
- Hydrostatic Testing: Ensures pipes can withstand high-pressure fluids.
- Dimensional Checks: Verifies compliance with specified tolerances.
- Rigorous testing is conducted to ensure the pipes meet industry standards. Tests include:
-
Packaging and Dispatch:
- Pipes are cut to length, bundled, and securely packaged to prevent damage during transportation.
Applications
Stainless steel pipes are versatile and used in:
- Construction: For structural supports, handrails, and plumbing.
- Automotive: In exhaust systems and fuel lines.
- Oil & Gas: For transporting corrosive fluids and gases.
- Food and Beverage: For sanitary applications in processing plants.
Advantages
- Corrosion Resistance: Ideal for harsh environments.
- Strength and Durability: Long-lasting and resistant to wear and tear.
- Aesthetic Appeal: Suitable for visible installations.
- Eco-Friendly: Fully recyclable, contributing to sustainability.
Conclusion
The manufacturing of stainless steel pipes is a blend of advanced technology, precision engineering, and adherence to stringent quality standards. These pipes play a pivotal role in modern infrastructure and industrial applications, making them an essential component of global development.